Vacuum dryers are a multifaceted product used in a wide variety of processes in the food, chemical, pharmaceutical, and plastic industries. Vacuum dryers work to remove liquids from materials or to change a material’s molecular and physical chemistry. It removes liquid by heating the material through conduction and vaporizing the liquid. Vacuum dryers can change molecular and physical chemistry through chemical reactions and solid-state polymerization. These processes are thermal and do not involve mechanically separating the liquid from the material.
The vacuum drying system consists of a vacuum dryer, media heating and circulating, vacuum, and solvent recovery components. The dryer is the centerpiece of a vacuum and consists of an enclosed, thermal-jacketed vessel which is usually constructed of stainless steel. The hot media flows through the dryer’s circular jacket and transfers heat to the drying chamber. In a vacuum dryer, a vacuum line runs from the dryer to the source, usually a pump, which reduces the dryer’s atmospheric pressure. This line pulls off the vapors as they exit the dryer while the wet material dries. These vapors are then captured by a condensing system located between the vacuum source and dryer.
Vacuum drying can provide several benefits. Because vacuum drying controls atmospheric pressure, it reduces the boiling point required to remove the liquid. By controlling the pressure and reducing the boiling point, the material can be dried at a faster rate. This makes vacuum drying suitable for products that are heat sensitive. Hazardous materials are also suitable for vacuum drying. Dangerous chemicals or solvents are contained by the vacuum dryer without any threat to the outside atmosphere. Although vacuum drying can be quite beneficial, the heat transfer temperature is limited in comparison to direct-heat drying.
Vacuum dryers can offer two separate processes: batch and continuous. Most vacuum dryers operate under batch processing because of the dryer’s sealing requirements. Batch-processing is versatile and can be easily adapted to changing manufacturing processes. Vacuum dryers that operate under a continuous process can be made into a hybrid-batch-continuous process by installing additional equipment.
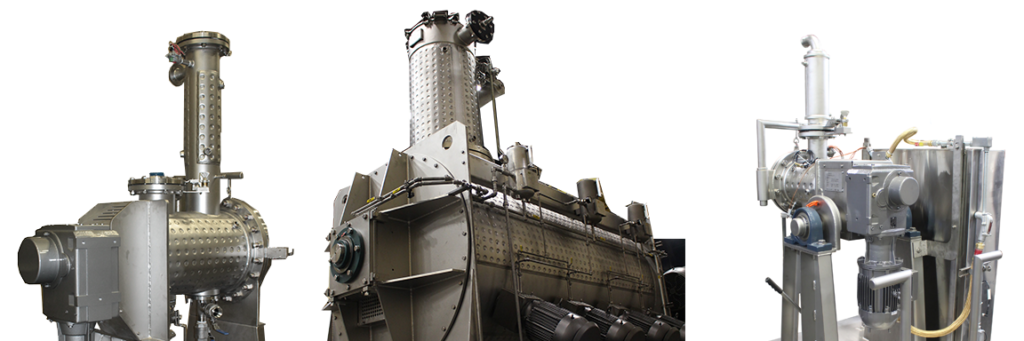
Processors have been searching for a more efficient vacuum dryer to better control their particle size and reduce the processing time. To answer these specific needs, Processall has developed the U-Max Dryer. The U-Max Dryer utilizes a mechanically fluidized bed mixing action complimented by the independent high-speed chopper/mills. The Processall mechanically fluidized bed principle is generated by the rotation of a shaft within the confines of a horizontal cylinder. Permanently affixed arms with plow-shaped agitating elements extend from this shaft. Material is constantly moving in axial and radial motion. The constant folding action is caused by the plow-shaped agitator elements with their overlapping paths. This assures constant mixing of material with each rotation. Each U-Max Dryer is designed for a specific Froude Number to maximize mixing and heat transfer efficiency.
The U-Max Dryer provides the customer with the following advantages:
- Reduced cycle time: Achieving a higher “U” factor to our Mechanical Fluidized Action complimented by the dryer’s chopper/mills reduces the cycle times.
- Particle size control: High-speed chopper/mills control the size of the particles and by utilizing the energy input the units provide the same particle size distribution batch after batch.
- Better temperature control: The dryer has a superior jacket design to control the heating media flow and eliminate hot or cold spots which combine with the Mechanical Fluidized Action to control the product temperature.
- Multi-step operations: Reaction, mixture, liquid dispersion, and granulation are just a few of the dryer’s capabilities.
- Reduced material handling: Processall handles multiple operations to reduce the number of times the product needs to be moved or conveyed.
- Moisture control: The Mechanical Fluidized Action and the particle size control of these dryers allow for manufacturers to receive the same percentage of moisture or solvent levels batch after batch.
Processall also maintains a fully equipped testing facility in Cincinnati, Ohio designed to provide customers with the data they need to develop their process, scale up to full production and identify the ideal Processall equipment and features to achieve the highest quality product at the desired production volumes. We extend an open invitation to all potential customers to bring their products to our test center and get a “hands-on” experience with our technology and capabilities.
We also maintain a rental fleet that customers can utilize to do further testing at their facility or employ to minimize their startup costs for a new process.
Contact us today with all your vacuum drying questions and our experienced industry professionals will help you find the right mixing solutions for your particular application.