According to market research, the global growth rate for mining is over 10%, and the industry is projected to grow into a 2.0 trillion-dollar market at the end of 2022. Industrial mixing equipment provides critical solutions to the mining industry.
Mining companies have found plow mixers vital in everything from the beginning of the refining process to the final stages of production.
- Iron refiners use plow mixers to pelletize iron ore to improve its flow properties before it is liquified to begin the conversion into steel.
- In the aluminum industry, pretreat the bauxite with chemicals before the extraction of the aluminum occurs.
- Coal producers have even done work to convert coal ash into a viable fuel source by using plow mixing technology to agglomerate the dust back into the furnaces.
Processall’s employees have a long history of working with the mining industry aiding in everything from discovering new methodologies of processing mined materials, installing the unit, and maintenance throughout the life cycle of the machinery.
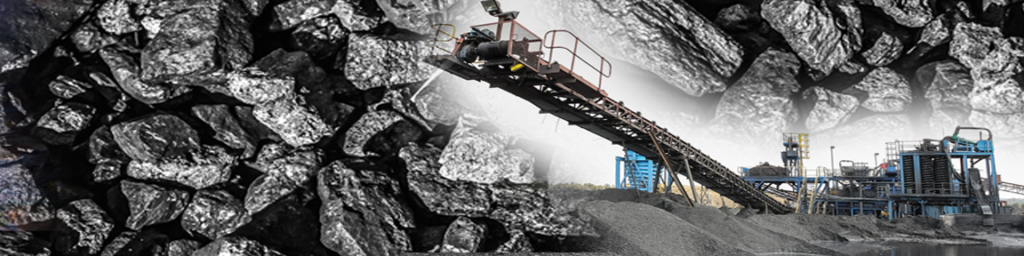
Processall’s plow mixers technology gives mining companies a leg up on the competition. Below are some benefits of moving toward horizontal mixers for mining applications.
- Able to be customized to be a U1 pressure vessel dependent on the customer’s needs
- The ability to agglomerate materials using spray nozzles and plow blades ensures materials adhere together.
- A high-speed mix improves the rate chemical of reaction
- Vessel jacket allows different media (hot oil, steam, or tempered water) to be used depending upon the thermal sensitivity of the product
- Ability to also serve as a drying vessel due to the high heat transfer rates
- Ability to adjust between high pressure and low pressure depending on the steps in the process
- A vacuum lowers the vapor pressure of the liquid, facilitating quicker drying times.
- Thermal jackets to allow for optimal temperature controls
- High-speed mix which can handle materials as fine as dried oats without damaging the material
- Easy to scale up and predict mix, reaction, and drying times after lab testing
- Ability to remove water or organic solvents from material
- Vessels can be outfitted to increase versatility:
- Mechanical seals – will allow the vessel to be pressurized as well as reach a low vacuum (28 Hg)
- Liquid lances – will enable media to be sprayed onto the substrate
- Ability to perform the reaction, mixing, and drying within one unit resulting in:
- Faster throughputs
- Reduced energy consumption
- Smaller footprint on the production floor
Mining Operations using plow mixers technologies
- Iron Ore
- Refining Bauxite
- Clay
- Talc
- Calcium Carbon
- Limestone
- Gypsum
- And many more
Processall maintains a fully equipped testing and manufacturing facility in Cincinnati, Ohio. We can provide customers in our laboratory with the data they need to develop their process, evaluate equipment, scale up, and identify the necessary solution to maintain desired production volumes. We invite potential customers to bring their products to our test center and get a “hands-on” experience with our technology and capabilities.
We also maintain a rental fleet that customers can utilize to conduct further testing at their facility to minimize their startup costs for a new process.
Don’t hesitate to contact us with all your material processing questions; our experienced professionals will help you find the right industrial mixing equipment solutions for your particular application.