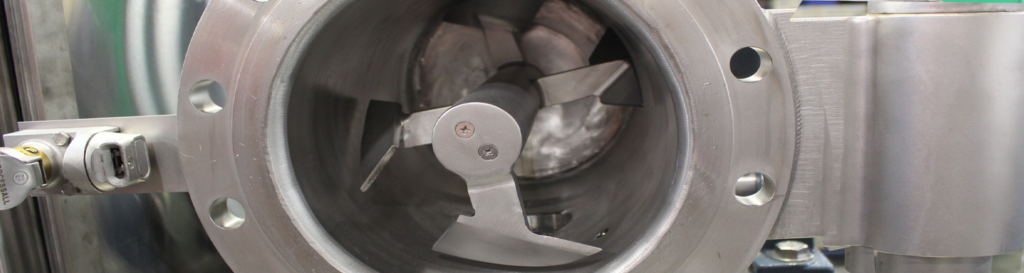
Testing Services
We Look Forward to Facilitating the Testing of your Specific Application
Processall’s testing facility in Cincinnati, Ohio is a modern, well-equipped facility designed to provide you with the data you need to develop your process, evaluate our equipment, and scale up to the production size equipment you intend to purchase. We can run batches in sizes from 1 to 25 gallons and perform accurate mixing, granulating, drying and reacting tests. The typical test takes from 1 to 3 days and may include runs on several different pieces of equipment.
Three mixing and drying units are available for testing
your specific application:
1. Model 4 H/V – 2.8-liter capacity (0.7 gallons),1 ½ HP main drive, 2 HP mill drive Mixer/Reactor/Dryer with heating/cooling jacket. The unit is rated for vacuum operation.
2. Model 140 H – 100-liter capacity (26 gallons) 10 HP main drive, 10 HP mill drive. Mixer/Dryer with heating/cooling jacket. Jacketed filter for vapor disengagement. The unit is rated for vacuum operation.
3. Model 4 H/P – 2.8-liter capacity (0.7 gallons),1 ½ HP main drive, 2 HP mill drive Mixer/Reactor/Dryer with heating/cooling jacket. The unit is rated for Internal pressure of 200 PSI and full vacuum operation.
What do I do to initiate a test?
First, contact your Processall representative to secure a test date. Typically, test dates are attained two to six weeks in advance so that arrangements can be made and materials acquired. In order to insure strict confidentiality, we only schedule one customer in at a time; therefore space is limited. Secondly, we encourage you to prepare a syllabus describing the tests you wish to perform, including batch sizes, recipes, sampling procedures, time involved, etc. We can better serve you when we are prepared in advance
and this allows us to review the procedure prior to test day.
Material handling & support equipment
1. Large Vacuum System –
5 HP vacuum pump with condenser and jacketed holding tank for drying and solvent recovery.
2. Vacuum Drying Filter –
Jacketed filter for use on mixers and dryers.
3. Liquid Dispersion System –
Pressurized tanks and peristaltic pumps for spraying liquids into the process.
4. Oil Circulation System with Heating and Cooling capabilities.
5. Recirculating Hot Water System
6. Compressed Air
7. Steam Generator
8. Digital Scales ranging from .0001 lb to 250 Lb
9. Analytical scale available for more accurate
minor ingredients
10. Other Instruments such as moisture measuring balance,
microscope, pressure and vacuum transducers…etc.
What is the charge for the tests?
Starting at $5,000 per day
Contact us for multi-day testing discounts
Storage of leftover raw materials and test products
Any raw materials or test product left for future testing will incur storage fees after 30 days following testing date at a rate of $500 per month.
Special Charges
• Horsepower checks
• Extensive cleanup or set up charges can be assessed
based on customer information provided
*Fees will be applied towards the purchase of a new unit over
$100,000 within a year of the testing date.
What do I do I need to provide?
First, and most importantly, all materials required for
performing your process. Remember that several tests may be run, so be sure to provide enough supplies to avoid
running short. We will need sample containers adequate
for preparing your samples and returning them to your
facility. Please provide shipping instructions and labels for
returning these samples. Finally, please provide us with all shipping labels, MSDS forms and warnings required to meet DOT requirements when returning your product. Your
product will be sent back “freight collect” unless other
arrangements are made in advance.
Customer Testimonial
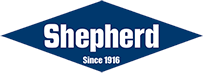
“As part of our new product development process, we utilized Processall’s plow tilt-a-mix mixer under their laboratory rental and product testing programs. We took advantage of their larger plow tilt-a mixer to manufacture kilogram scale quantities of a development product needed for customer testing. The Processall team is very knowledgeable and responsive to our application needs.”
-Mark Scott, Senior Development Engineeer, The Shepherd Chemical Company