When most people hear ceramics, they envision pottery; however, the Ceramics market is widely diverse. It touches everything from semiconductors to aerospace to medical devices. Each of these industries requires different base materials to be used to produce the ceramics—materials used in the industry range from sand to alumina oxides to bentonite. Additionally, with the advent of new ceramic matrixes like transparent aluminum, the ceramics market is poised to continue growing at 8 percent annually.
Due to the variety of different ceramic materials manufacturers encounter when producing ceramics, the blend mixing process of the powders is becoming more vital. More and more customers are tightening tolerances for high-end ceramics, and manufacturers need to ensure they meet higher levels of consistency. In industries like the microchip industry, nanometers on ceramic capacitors determine the level of success or failure. For this reason, uniformity of the mixture is becoming vital for ceramics. Processall’s technology team has worked with many powder blending operations before. One situation reduced the mixing time from 8 hours to 30 minutes and improved powder uniformity. Additionally, Processall’s horizontal mixers enable companies to coat materials as fine as 200 nanometers. This plow mixing technology allows ceramics makers to have binders added to the powders ensuring that they will better adhere together.
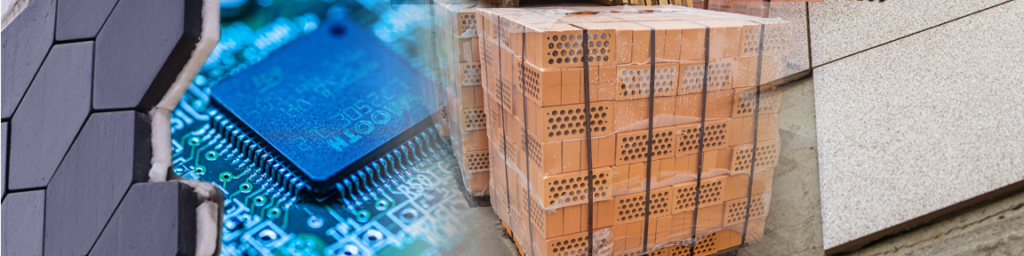
Processall’s employees have a long history of working with the ceramics industry aiding in everything from initial testing to installation of the industrial mixing equipment to maintenance throughout the life cycle.
Processall’s Plow Mixing technology gives manufacturers a leg up on the competition. Below are some benefits of moving toward plow mixing technologies for ceramics industry applications.
- The fluidized bed created by the mix creates greater uniformity in the compounds.
- Customers can potentially observe a 600% increase in production by moving to a plow mixer from a ribbon blend.
- Even with the high horsepower, Processall could verify a reduced energy consumption at a constant production rate vs. a ribbon blender.
- Being thermally insulated, the unit did not cause any temperature spikes in mixing the material.
- Ease of cleaning to be able to transition from one blend to another
- Reduced Safety concerns over other mixing technologies
- The vessel jacket allows different media (hot oil, steam, or tempered water) to be used depending upon the thermal sensitivity of a product.
- Easy to scale up and predict mix and coating times after lab testing
- Ability to remove water or organic solvents from material
- Vessels can be outfitted to increase versatility:
- Mechanical seals – will allow the ship to be pressurized as well as reach a low vacuum (28 Hg)
- Liquid lances – allows media to be sprayed onto the substrate.
- Ability to perform the reaction, mixing, and drying within one unit resulting in:
- Faster throughputs
- Reduced energy consumption
- Smaller footprint on the production floor
Current Applications of Ceramics
- Pottery
- Heat-resistant tiles for Aerospace
- Resistor and Capacitors for Microchips
- Transparent Aluminum
- Dentures
- Bricks
- Cutting tools
- Femoral head implants for hip replacement
- Abrasives
- Flooring
- And many more
Processall maintains a fully equipped testing facility in Cincinnati, Ohio. It is designed to provide customers with the data they need to develop their process, evaluate equipment, scale up, and identify the necessary equipment to maintain desired production volumes. We invite all potential customers to bring their products to our test center and get a “hands-on” experience with our technology and capabilities.
We also maintain a rental fleet that customers can utilize for further testing at their facility or minimize their startup costs for a new process.
Please feel free to contact us with all your material processing questions, and our experienced industry professionals will help you find the right industrial mixing equipment solutions for your particular application.