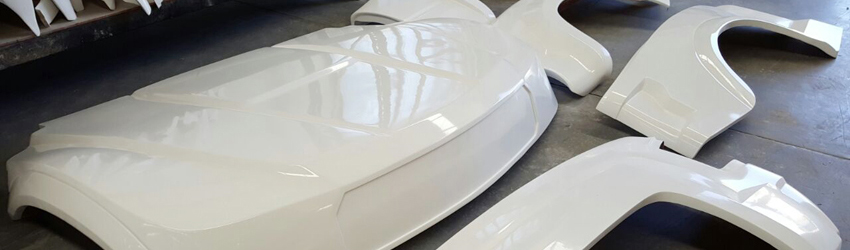
Bulk Molding Compounds
The Processall Mixer with its plowshaped agitators has given outstanding performance
in the mixing of powders, viscous and fibrous and powdered materials used in the
manufacture of bulk molding compounds
Bulk Molding Compound (BMC) typically consists of the following ingredients: polyester resin, catalyst, modifier, fillers, pigments, and fiberglass fibers of different lengths. Bulk molding compounds provide
superior performance characteristics include:
• Excellent mechanical properties
• Electrical and chemical properties
• Weather resistance
• High strength per weight ratio
• Flame resistance capabilities
• Superior flow characteristics
when conforming to a mold

Traditional mixing technology used in BCM production involves the use of two machines: A high-speed dispenser to prepare the heavy, viscous paste, and a high-shear sigma blade to mix the fibers. This two-step process has
created many problems, such as inadequate dispersion of paste, fiber opening, additional material/handling steps, and loss of styrene vapors. Additionally, the fibers tend to break under the shear of the sigma
blade and processing dispersion is compromised, causing inferior physical properties in the compound.
Typical applications that these are used are in:
• Automotive Industry
• Appliance Components
• Power Tool Housings
• Computer Components
• Electrical Fixtures
• Dishware
Plow mixers have the capability of adjusting to the degree of mixing by using the mills in conjunction with the main mixing elements. These mixing elements working in union with each other provide thorough
intensive mixing for preparing the paste and efficient, low shear, gentle mixing to add the reinforcing fiber to resin. These are all within the confines of a single vessel.
The ability to mix the entire batch in a single vessel, without additional material handling steps, reduces cost and makes the system more adaptable to automation. Special large discharge doors found on the plow mixers are used to remove the material efficiently, eliminating manual labor. Discharge of the mixer is fulfilled by opening the discharge door and operating the mixer.
Processall mixers are easily cleaned by adding solvent with scrubbing agent, and operating the machine for short periods, then discharging. The mixer can process fibers anywhere from 1/8” to ½” in length at loading levels from five to 50%. Typical mix cycles are in the 5 to 10 minute range. The ideal mixing practice produces evenly coated fibers in the product. The material is easy to handle, with less bulky density than that normally is produced by other mixing processes. Besides fiberglass, a wide variety of high-tech reinforcing fibers have been developed. Processall is a leading provider of chemical-processing plow mixers, reactors, dryers, sterilizers, and extractors. Should you have any questions about your process, please contact one of our experts.
Processall maintains a fully equipped testing facility in Cincinnati, Ohio designed to provide customers with the data they need to develop their process, evaluate equipment, scale-up and identify the necessary equipment to maintain desired production volumes. We extend an open invitation
to all potential customers to bring their product to our test center and get a “hands on” experience with our Technology and capabilities. We also maintain a rental fleet that customers can utilize to do further testing at their facility or employ to minimize their startup costs for a new process.