With the increasing population worldwide and reduced land usage for farming due to factors like urban sprawl, the demand for effective agrochemicals is on the rise. Currently, many companies in this arena are facing a wide variety of other external challenges too. Many of these challenges are directly tied to people’s concern about the usage of chemicals in their food and general fears of what they may do over the years to people’s bodies. However, farmers are also concerned about the increasing resistance of pests to agrochemicals. Add to this the Covid 19 pandemic last year and many analysts project the world to see some food shortages globally due to manufacturing plants being down last year. These external pressures are putting extra focus on the agrochemical industry and many companies in this arena are looking to improve their manufacturing processes.
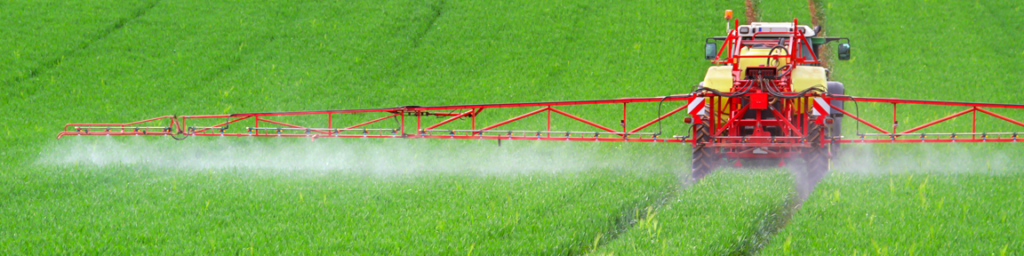
One of the most common steps in the making of agrochemicals is the drying and evaporation of volatile chemicals from the final product. Processall’s plow mixers have been involved with the drying operations in the agrochemical industry for some time whether it be removals of water or organic compounds. They have helped manufacturers of herbicides, pesticides, fungicides, and fertilizers with these drying operations. Products in this arena need to meet very tight specification levels set forth by the EPA and FDA with regulations on everything from Volatile Organic Compounds to hazardous chemicals measuring sometimes as low as parts per billion. It is for this reason that drying of compounds and removal of hazardous chemicals is vital to this industry. Additionally, blending operations are common in the agroindustry because farmers often want materials that have multiple properties when applying chemicals to their fields. Whether it be blends of dry powders or liquid dispersed compounds plow mixing technology has been shown to aid companies in this arena. Plow mixers can be also fitted with chopper blades which can help reduce the particle size of the granular materials. Processall’s technical team has additionally worked with companies to convert spent sewage and animal manure to be used as a natural fertilizer. Plow mixers have done this by serving as the vessel for reacting bases like caustic with the manure. Plow mixers can then concurrently dry the material reducing the need for multiple unit operations on site. Plow mixers have been shown to be even able to encapsulate agrochemicals which allow for materials to be time released into the soil and crops.
Processall’s employees have a long history of working with the agrochemical industry aiding in everything from initial testing to installation of the unit to maintenance throughout the life cycle of the unit.
Processall’s Plow Mixing technology gives manufacturers in the agrochemical arena a leg up on the competition. Listed below are some of the benefits of moving toward plow mixing technologies for agrochemical applications.
- The fluidized bed created by the mix gives a high heat transfer coefficient for drying and extraction of hazardous materials
- Being thermally insulated the unit does not cause any temperature spikes when performing drying operations
- Ease of clean to be able to transition from one product to another
- The fluidized bed creates greater uniformity in the mixes
- Customers can potentially observe upward of a 600% increase in production by moving to a plow mixer from a ribbon blender on dry blending operations.
- Ability to disperse powder into the liquid mixes
- Able to be manufactured to become a U1 pressure vessel for reactions
- Able to react materials together in a fluidized bed speeding up the rate of reaction for materials
- Ability to encapsulate materials and enable agrochemicals to have time-released properties
- Vessel jacket allows different media (hot oil, steam, or tempered water) to be used depending upon the thermal sensitivity of the product
- Optional chopper blades can help reduce particle sizes
- Ability to adjust between high pressure and low pressures depending on the steps in the process
- High-speed mix that is gentle enough to mix material as fine as dried oats without damaging the material
- Easy to scale up and predict mix, reaction, and drying times after lab testing
- Ability to remove water or organic solvents from material
- Vessels can be further outfitted to increase versatility:
- Mechanical seals – will allow the vessel to be pressurized as well as reach low vacuum (28 Hg)
- Liquid lances – allows media to be sprayed onto the substrate
- Ability to react, encapsulate, granulate, mix, and dry materials within one unit resulting in:
- Faster throughputs
- Reduced energy consumption
- Smaller footprint on the production floor
Agrochemical materials using plow mixers
- Herbicides
- Pesticides
- Fungicides
- Fertilizers
- And many more
Processall maintains a fully equipped testing facility in Cincinnati, Ohio designed to provide customers with the data they need to develop their process, evaluate equipment, scale up, and identify the necessary equipment to maintain desired production volumes. We extend an open invitation to all potential customers to bring their product to our test center and get a “hands-on” experience with our technology and capabilities.
We also maintain a rental fleet that customers can utilize to do further testing at their facility or employ to minimize their startup costs for a new process.
Please feel free to contact us with all your material processing questions and our experienced industry professionals will help you find the right mixing solutions for your application.