Joint Replacement surgery has become a highly routine surgical procedure over the past 20 years. Over 600,000 of these replacements are done annually in the United States alone. The manufacturing of these replacement joints is growing at 7% globally. Many factors contribute to this growth in needing joint replacements. Everything from bacterial infections, STDs, the aging population, obesity, and even the rise of high-impact sports play a part in the arthritic degradation of joints. For these reasons, many in the medical community believe this procedure will become even more routine with time.
Most joint replacements are currently made from ceramics, metals, and polymers. Still, the digital modeling and 3D printing revolution represent the beginning of a paradigm shift in this joint replacement market. No longer will joint manufacturers and doctors create universal options for human joint replacements. They are now prepared to better customize the replacement joints to better fit the individual, improving their effectiveness. Research is even being conducted to combine stem cell technology with 3d printed biodegradable polymers. Preliminary works are promising in replacing and regrowing these joints in the human body with this technology. With this projected revolution in the joint replacement market, many companies need to start planning and looking for improved manufacturing methods to take advantage of this golden opportunity.
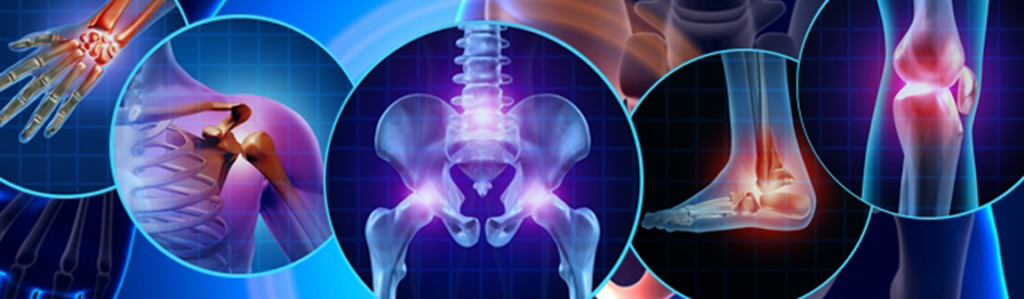
Plow mixing technology is currently used in various applications that directly affect the manufacturing of joints. Now, corporations in the biomedical joint arena use plow mixing to do everything from ceramic materials blending to polymeric materials blending. Ceramics producers use this style of mixing because of the high level of homogeneity of powders. The polymeric joint makers have found plow mixers one of the few mixers capable of mixing and dispersing the materials required to help produce ultra-high molecule weight polymers. Companies within this market also view these mixers as giving their corporations a competitive advantage because of the increased production rates.
Processall’s employees have a long history of working with the biomedical industry, aiding in everything from initial testing to installation to maintenance throughout the unit’s life cycle.
Processall’s Plow Mixing technology gives manufacturers in the joint replacement arena a leg up on the competition. Below are some benefits of moving toward plow mixing technologies for biomedical applications.
- Units can be thermally insulated, eliminating any temperature spikes from occurring when blending materials
- Ease of cleaning to be able to transition from one product to another
- The fluidized bed creates greater uniformity in the mixes
- Customers can observe an upward of 600% increase in production by moving to a plow mixer from a ribbon blender on dry blending operations.
- Ability to disperse powder into the liquid mixes
- The vessel jacket allows different medias (hot oil, steam, or tempered water) to be used depending on the thermal sensitivity of a product
- Optional chopper blades which can help reduce particle sizes
- Ability to adjust between high pressure and low pressure depending on the steps in the process
- High-speed mix that is gentle enough to mix material as fine as dried oats without damaging the material
- Easy to scale up and predict mix after lab testing
- Vessels can be further outfitted to increase versatility:
- Mechanical seals – will allow a vessel to be pressurized as well as reach a low vacuum (28 Hg)
- Liquid lances – allows media to be sprayed onto a substrate
Artificial Joints currently being produced in the biomedical arena
- Knee
- Pelvis
- Ankle
- Shoulder
- And many more
Processall maintains a fully equipped testing facility in Cincinnati, Ohio. It is designed to provide customers with the data they need to develop their process, evaluate equipment, scale up, and identify the necessary equipment to maintain desired production volumes. We invite all potential customers to bring their products to our test center and get a “hands-on” experience with our technology and capabilities.
We also maintain a rental fleet that customers can utilize to do further testing at their facility or to minimize their startup costs for a new process.
Don’t hesitate to contact us with all your material processing questions, and our experienced industry professionals will help you find the right mixing solutions for your particular application.