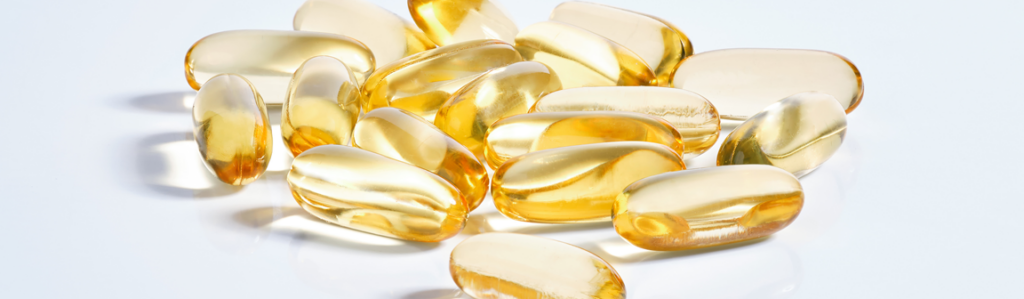
Encapsulation
Processall equipment is suitable for microencapsulation of
different products in the same machine without the use
of high temperatures and excessive energy consumption
The material to be coated is called the core or fill. The coating material is called the shell or wall material. This deposition can be single or more layers of different thickness.
Other coating techniques deposit one or more layers of different thicknesses using a spray dryer. These are very costly to maintain and operate due to the energy required to dry a liquid slurry and the large space necessary for this style of equipment. Also, it is possible to lose certain low boiling liquids when encapsulating heat-sensitive materials and other degradable ingredients using this method.
The Processall coating technology completely solves these issues by coating the dry core material with atomized layers of product dissolved in a solvent or water, mixed with binders such as cellulose derivatives, dextrins, emulsifiers, protein derivatives, starch derivatives, clay, lime or other chemicals. The product is tumbled to allow even distribution of coating. Other dry powders can be deposited continuously as the coating layers are added. A drying step can follow to quickly flash off the moisture under vacuum to maintain a low temperature processing and avoid product degradation.
Typical applications:
• Enhance stability of flavors and spices and
improve resistance to oxidation and clumping.
• Improve solubility and flowability of natural colors.
• Sweeteners can be protected from moisture
exposure to prolong sweetness perception.
• Vitamins and minerals can be coated.
• Ingredients can be protected against high
temperature exposure during baking.
• Sodium chloride can be encapsulated with
hydrogenated vegetable oil to prevent color
degradation, rancidity, water absorption,
and yeast growth.
• Chemicals and powders can be coated to enhance
flow-ability and protect against environmental
exposure.
The microencapsulation is generally
needed for the following reasons:
Stabilize core material
Protect sensitive core material and improve flow properties
Control rate of core release if this feature is required
Mask or preserve flavors and aromas
Protect leaching of core material to the environment
There are many additional applications for this technology.
For more information, contact Processall and send your product for testing at Processall’s
fully-equipped lab. We also offer a fleet of rental equipment for in-house product testing.