When most people think of the modern pharmaceutical industry, they think back to Sir Alexander Fleming discovering Penicillin in 1928. However, the roots of this industry date back to ancient civilizations including the Egyptians, Greeks, Chinese and Native Americans. These ancient cultures used plant extracts and herbal remedies to cure various ailments. Over time, knowledge of the medicinal benefits of these many commonly available materials grew. By the time of the Middle Ages, early pharmacies began to emerge in both the Muslim world and Europe where pharmacists began to dispense a wide variety of materials to treat ailments. Some of these early treatments were borderline comical to us using today’s medical standards. In fact, materials like arsenic and mercury were used to treat syphilis in the early days of medicine. Still these early pharmacies helped further advance medicine for future generations. By the age of the Renaissance with the scientific method becoming more refined, data not hearsay began to be used more often in people’s medical decisions.
By the time of the 1930s, many discoveries had been made in this field, but it still was nowhere near what it is today. The discovery of penicillin is still widely regarded as one of the most landmark discoveries in medical history. Not only did science finally discover a method to stop the growth of many bacterial infections, it also helped lay the foundation for many future medical advancements. This new family of drugs created from Penicillin and the ensuing Nobel Prize for medicine led to many entrepreneurs and businesspeople to take more economic risks in search of the next wonder drug. This large economic infusion helped fund further scientific and technological advances in the medical field. Following World War 2, this market legitimately exploded over night and has evolved into a 1.5 trillion dollar market in 2022 which is still growing at a 9.1% clip annually.
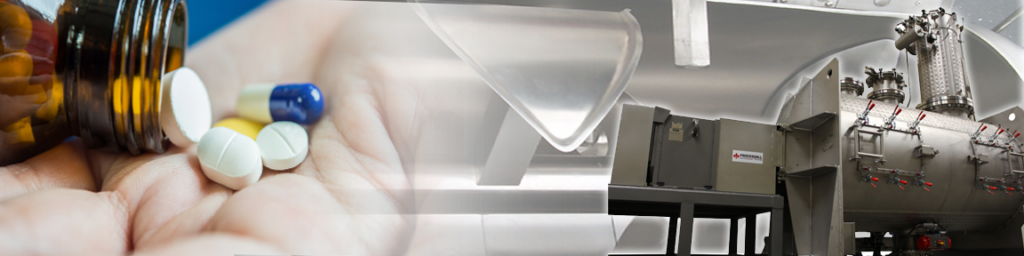
The reason for this increased need in pharmaceuticals is multitiered. One reason is people are living longer and need more medicines to maintain the same quality of life. However, at the same time drug resistant bacterial infections are becoming more common. Additionally, the globe is becoming more interconnected and travel between locations on opposite sides of the earth is becoming more necessary. This interconnectivity of society has created the obstacle of mitigation of travel no longer being viable in certain disease outbreaks. Covid-19 taught the world that. There are many other factors that contribute but this market segment and the demand for drugs will continue to grow into the future for decades for these reasons and many more.
As a result of these market pressures, many pharmaceutical companies are constantly in search of new technologies to improve their process. One of the technologies that this expanding market came to depend on is the plow mixers. Many pharmaceutical manufacturers quickly found plow mixers offered higher uniformity in the mixes than other technologies on the market. It can also create a liquid and powder dispersion. Plow mixers utilize a high-speed motor which creates a mechanically fluidized bed inside the vessel. This improves the final products uniformity and increases companies’ productivity when mixing. Plow mixers can also be accessorized with a chopper system. Choppers not only give additional mixing action but also can serve to help with wet granulations, particle coatings and encapsulations, improved particle size distribution, and drying. However, it is advised that lab test should always occur before determining if a chopper system is necessary.
Listed below are some of the most common additional options that can be used on plow mixers. However, all Processall Plow mixers are custom designed to meet the customers required specifications.
- Heating and cooling jackets that enable the mixer to also serve to heat and cool products to desired temperatures.
- Vacuum Stacks and Vacuum systems with condensers to enable the mixer to serve as a high-speed dryer for products that require tight temperature controls before thermal breakdown occurs.
- Thicker drums to enable the vessel to operate not only as a vacuum system but also a pressure vessel. ‘
- Coating on the mixer blades to reduce wear and improve overall longevity.
- Sensors like VFDs, thermocouples, pressure indicators, Vibration sensors, Moisture sensors, smoke detectors, and many more to enable better tracking of what is occurring within the vessel. These sensors can then be equipped to be integrated into a company’s internal intranet, but it can also be used for cloud based applications and data tracking.
Many pharmaceutical companies buy plow mixers because of the versatility of features these machines offer but they also offer many other benefits. Some of the most common of these benefits clients have found are listed below.
- Ability to conduct multiple unit operations in one vessel.
- Reduced risk of contamination due to unnecessary handling
- Reduced overall footprint
Processall’s Plow Mixing technology gives chemical manufacturers a leg up on the competition. Listed below are some of the benefits of moving toward plow mixing technologies for chemical manufacturers.
- High heat transfer rate with coefficients upwards of 50 BTU/(hr•ft²•°F) which increases the speeds of drying
- Lower vaporization temperatures protect thermally sensitive material
- Can be customized with a wide variety of safety features to improve employee safety when handling dangerous materials
- Ability to serve as both a reactor and dryer of materials thus reducing the need for multi-unit operations. (Many stearate manufacturers use plow mixers because of these features)
- VFD motors enabling wide levels of control for the overall mixer speed
- Can be customized to include pulse back filters to reduce product loss during drying
- Thermal jackets to allow for optimal temperature controls.
- Ability to serve as a U1 pressure vessel
Processall maintains a fully equipped testing facility in Cincinnati, Ohio designed to provide customers with the data they need to develop their process, evaluate equipment, scale-up, and identify the necessary equipment to maintain desired production volumes. We extend an open invitation to all potential customers to bring their product to our test center and get a “hands on” experience with our technology and capabilities.
We also maintain a rental fleet that customers can utilize to do further testing at their facility or employ to minimize their startup costs for a new process.
Please feel free to contact us with all your material processing questions and our experienced industry professionals will help you find the right mixing solutions for your particular application.